ASSEMBLY:
All Silos are delivered clean and in working order. Please follow the steps below to make efficient and safe use of the silo on your job site.
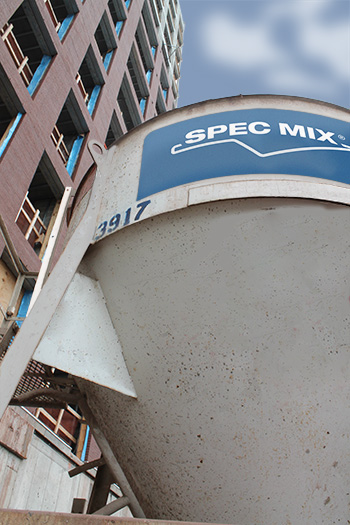
STEP 1:
- Select an area on the job site where the ground is firm level and stable. Place silo in a downwind position where product dust will not disperse into operator.
- Insert forks completely into fork tubes to move the silo (Standard Forklift Required – 26 Ft 4500 lb capacity)
- Secure third contact point with a chain or strap (5,000 lb Working Load). This prevents the silo from sliding off the fork tubes during transport.
- Place silo on the approved location
- Lower ladder, allowing access to the safety railed platform
- Attach safety ring and dust curtain on the top of the silo. Only do this when silo is not in raised position. Follow all OSHA job-site regulations.
STEP 2:
- Raise tower to the desired height until the holes in the silo leg match the holes in the receiver tube assembly.
- Using the double leg pins attached to the frame, secure the upper silo assembly by sliding the leg pins into position. Stand outside of the perimeter of the silo
- Secure the pins with the safety hitch pins.
- Repeat process for all four sides.
- Attach the slide gate handle in its place, matching the short handle to the gate door and the long handle to the pivot point located on the cross brace.
STEP 3:
- Attach all warning signs and secure the silo at the job site. Make sure silo is ready to load.
- Prepare to load bulk bags into the silo. Visually inspect the bulk bag, check for fraying on loops and bag – If conditions exist DO NOT ATTEMPT TO LOAD BAG – Call Us at (800) 724-8193
- Bulk bags are easily picked up by sliding forks through the bags reinforced loops. Once the bag is above the silo and in position, 2-3 inches above the safety ring, the laborer on the safety platform can release the bags contents by pulling on the bags closure pin on the bottom of the bag. Use the supplied SPEC MIX Safety hook.
- Make sure the bag does not touch the safety ring and always wear protective gear including dust mask, safety goggles, and gloves.
STEP 4:
- After the silo is loaded with product, place the batch mixer beneath the cone under the silo’s boot.
- If desired, trim the boot so the product goes directly into the mixer.
- To make product, add the desired amount of water to the mixer and pull back on the silo handle to dispense the amount of material needed to achieve the desired consistency.
- Let the product mix four to five minutes to ensure complete hydration of all materials for optimal workability and board life.
STEP 5:
- The SPEC MIX® silo system can easily be transported to multiple locations on your job-site, ensuring that you have the material where you need it, when you need it
- Lift up the silo and pin the legs in the upright position, transport to the new location (dry, level and stable ground)
- Place the silo and re-secure all leg pins and safety guards.
- Remember to follow all OSHA job-site regulations when working on the job-site.
- Call Package Pavement® today to learn more about the industry standard for mortar, grout, and stucco delivery on job-sites across America. (800) 724-8193
STEP 6:
- After job is complete, please make sure the silo is clean and there is no product remaining inside of it. Thank You for choosing SPEC MIX®
The SPEC MIX® Silo System is the ultimate contractor tool for maximizing the production and profitability of any workforce. The design is simple, yet highly efficient when producing dry, cement-based products on site. Whether the job is small or large, the system will greatly reduce the cost of labor and the amount of waste (sand, cement, paper bags) common with conventional batching methods. The silo is the cornerstone of our bulk delivery systems. Offered in various sizes and configurations, the SPEC MIX® silo is the most versatile silo system in use today. The gravity feed is not dependent upon pressurized water hook ups, electrical power or gasoline motors. Simply pull the slide gate handle and you’re making material.
SPEC MIX® silos are manufactured to hold a single 3,000 lb bulk bag, 5 bulk bags and 10 bulk bags. These options enable you, the contractor, to determine which silo system best suits your needs and job-site demands. Silos can be fitted with dust curtains, screw augers, set at various heights, and can be used with any mixer on the market to increase the productivity and efficiency of your job-site. For greatest efficiency place the silos near your work area so as your crew moves around the job site, the silos move as well making the most of your people and equipment. All silos operate easily and smoothly, eliminating the heavy lifting and twisting associated with the production of materials. Each silo comes with a bilingual operations and safety manual. We encourage you to follow it closely.